
25 warehouse KPIs to help measure performance
August 28, 2024
Managing a warehouse efficiently is crucial for any organisation, yet many businesses struggle to pinpoint what exactly they should be monitoring. Without a clear understanding of the key performance indicators (KPIs) that drive warehouse efficiency, companies often face issues such as delayed order fulfilment, increased operational costs, and decreased customer satisfaction.
These problems can have a cascading effect on your entire operation. Delayed orders frustrate customers, potentially leading to lost business. Inefficient inventory management can result in overstock or stockouts, tying up capital or failing to meet demand. Operational inefficiencies can inflate costs, eating into your bottom line and making it harder to compete. All these issues can create a stressful and chaotic working environment, making it harder to maintain high levels of productivity and safety.
To avoid these pitfalls and ensure your warehouse operates at peak efficiency, it's essential to track the right KPIs. In this blog post, we'll guide you through the critical KPIs you should be monitoring to enhance your warehouse performance. By focusing on these metrics, you'll be able to:
● Improve order accuracy and boost customer satisfaction
● Optimise inventory management to avoid overstock or stockouts
● Increase operational efficiency to lower costs
● Enhance labour productivity for better resource utilisation
● Maintain high standards of warehouse safety to protect your workforce
Join us as we explore each of these areas in detail, providing you with actionable insights and strategies to measure and improve your warehouse efficiency. By the end of this post, you'll have a comprehensive understanding of the KPIs that matter most and how to leverage them to drive continuous improvement in your warehouse operations.

KPIs to help monitor warehouse order accuracy and customer satisfaction
A high order accuracy rate means your customers are receiving the exact items they want and in perfect condition. With 65% of sales coming from existing customers, this is a key metric to be tracking for your warehouse.
Order picking accuracy
Order picking accuracy helps to measure the percentage of orders that are being picked accurately and without errors. This metric ensures high customer satisfaction by reducing the amount of returns that are made.
To track this metric, take the total number of picking errors made and compare them to the total number of orders picked. Implementing tracking at a basic level involves using a Warehouse Management System (WMS) to log orders and errors, conducting regular audits to verify accuracy, and providing feedback to staff on performance. Setting clear goals for accuracy and continuously reviewing and improving processes will help maintain high standards.
On-time shipment rate
This correlates to the number of orders shipped either on, or before the scheduled shipping date. This metric is critical for maintaining customer satisfaction. It also influences operational reliability.
To track this metric, measure the number of shipments dispatched on time versus the number of late shipments. Implementing this involves using a Warehouse Management System (WMS) to record shipping dates, monitoring daily dispatches, and comparing them against scheduled dates. Regularly review the data to identify delays, and provide feedback to improve processes and adherence to schedules. Setting clear benchmarks and continuously working towards them will help maintain high on-time shipment rates.
Shipping accuracy
Shipping accuracy tracks the number of orders you are shipping correctly. This includes both the correct items and the quantity of them. Shipping accuracy reduces the number of returns you’ll have to deal with and it also reduces the cost of reshipment.
To calculate this metric, take the number of orders accurately shipped and divide it by the total orders dispatched. To implement tracking, use a Warehouse Management System (WMS) to log each order and its accuracy, conduct periodic checks to verify shipping accuracy, and review the data to identify patterns of errors. Providing regular feedback to staff and setting targets for improvement will help maintain high shipping accuracy rates.
Perfect order rate
Perfect order rate warehouse KPIs track the percentage of orders you are delivering without any issues at all. This includes damages, inaccuracies or delays. High perfect order rates directly correlate to customer satisfaction and lower return costs.
To measure your perfect order rate, divide the number of perfect orders by your total orders and multiply by 100. Implementing this involves using a Warehouse Management System (WMS) to log order issues, regularly reviewing orders for damages, inaccuracies, and delays, and providing feedback to improve processes. Setting benchmarks and continuously monitoring performance will help maintain a high perfect order rate.
Rate of return
The rate of return is the percentage of orders that are returned by customers. If you have a high return rate then this can indicate that you have an issue with product quality or order accuracy.
To measure this, divide the number of returned items by your total shipped items and multiply by 100. To implement tracking, use a Warehouse Management System (WMS) to log returns, regularly review return data to identify trends, and address underlying issues. Providing feedback and making necessary adjustments to improve product quality and order accuracy will help reduce the rate of return.

KPIs to help monitor warehouse inventory management
Inventory warehouse management KPIs are useful for tracking how fast your current inventory is moving. It also allows you to see if your processes are running smoothly, and if any areas require improvement.
Inventory accuracy
Inventory accuracy pertains to how accurate your recorded inventory levels are, in comparison to your physical inventory. It’s important because it can prevent both stockouts and overstock situations, which has a direct impact on financial reporting.
To measure this KPI, conduct regular audits and compare the physical count with your system records. Implement tracking by using a Warehouse Management System (WMS) to record inventory, scheduling periodic physical counts, and reconciling any discrepancies. Regular reviews and adjustments based on audit findings will help maintain high inventory accuracy and ensure reliable stock levels.
Inventory turnover
Inventory turnover measures the rate at which your inventory is being sold and replaced over a set period. It’s important because it indicates how efficient you are at managing your inventory while detailing which products are selling the most.
To measure this KPI, divide the cost of goods sold by your average inventory value. This can be done over different periods to shed light on seasonal spikes or changes in demand. Implement tracking by using financial and inventory management systems to regularly update and review these figures, allowing you to adjust purchasing and inventory strategies accordingly. Regular analysis will help maintain optimal inventory levels and improve turnover rates.
Stockout rate
Stockout rate correlates to the frequency in which items are out of stock when they have been requested. High stockout rates can lead to lost sales, as well as decreased customer satisfaction.
To measure this, divide the number of stockouts by the total occurrences of consumer demand. Implement tracking by using a Warehouse Management System (WMS) to log stockout incidents and compare them against customer demand data. Regularly review this data to identify patterns and adjust inventory levels and reorder processes to minimise stockouts and improve availability.
Order fill rate
This is the percentage of customer orders that are fulfilled from in-stock items. It’s an important metric to track as it reflects both your fulfilment efficiency, as well as your inventory availability.
To measure this KPI, divide the number of fulfilled orders by the number of orders placed. Implement tracking by using a Warehouse Management System (WMS) to record order fulfillment and regularly review the data to ensure high fill rates. Adjust inventory management strategies based on these insights to maintain optimal stock levels and improve fill rates.

KPIs to help monitor warehouse operational efficiency
Operational efficiency KPIs are important as they give clarity on the stock you’re receiving, and how efficient you are at moving it.
Order lead time
Order lead time pertains to the time it takes you to receive an order, to it being shipped. It’s important as a shorter lead time can drastically improve customer satisfaction, as well as cash flow.
To calculate your order lead time, measure the time from when an order is received to when it is shipped. Doing this over multiple orders allows you to take an average. Implement tracking by using a Warehouse Management System (WMS) to log order receipt and shipment times. Regularly review and analyse this data to identify bottlenecks and improve processes, aiming to reduce lead times and enhance overall efficiency.
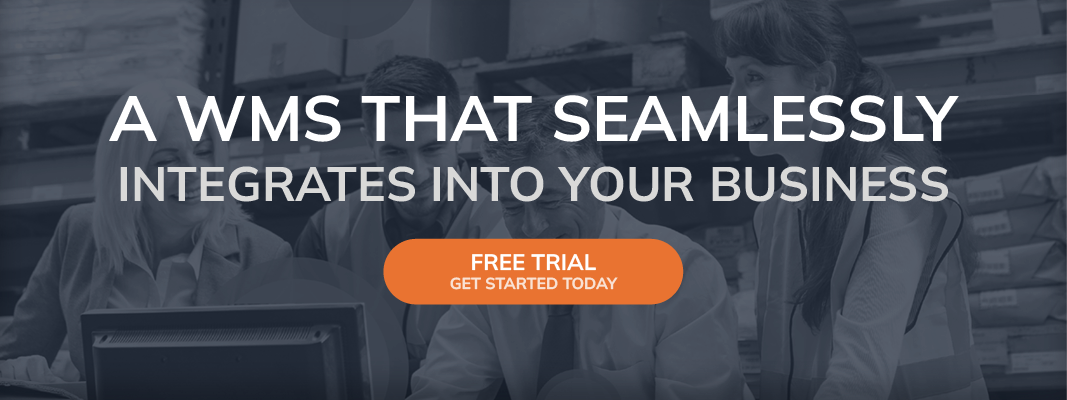
Order cycle time
Order cycle times track the total time it takes for someone to receive their delivery, after placing an order. It directly impacts customer satisfaction, as well as operational efficiency.
To track this metric, measure the time from when an order is placed to when it is delivered. Calculate this for individual orders, then take the average across multiple deliveries to gauge overall efficiency. Implement tracking by using a Warehouse Management System (WMS) to log order placements and delivery times. Regularly review this data to identify delays and improve processes, aiming to shorten the order cycle time and enhance customer satisfaction.
Dock-to-stock time
Dock-to-stock time is the time taken to move an item from the receiving dock to its location within the warehouse. If you have a short dock-to-stock time, this improves the general availability of items, while reducing potential bottlenecks.
To measure this metric, record the time goods are received and compare it to the time they arrive at their storage location. Implement tracking by using a Warehouse Management System (WMS) to log the receipt and storage times. Regularly review this data to identify inefficiencies and streamline processes, aiming to reduce dock-to-stock time and improve overall warehouse operations.
Receiving efficiency
Receiving efficiency is how long it takes to receive and process goods. It’s important as it reduces bottlenecks while increasing the flow of your warehouse. It also ensures that inventory is available to be picked and shipped, at all times.
To measure this metric, record the time taken to receive goods and compare it to previous periods to assess whether you're meeting targets. Implement tracking by using a Warehouse Management System (WMS) to log receiving times, and regularly review the data to identify areas for improvement. By continuously monitoring and optimising receiving efficiency, you can maintain a smooth and effective warehouse operation.

KPIs to help monitor warehouse cost management
Cost management KPIs are useful for identifying where costs can be reduced. It also gives you a good benchmark for improving your eCommerce efficiency from a financial standpoint.
Order processing cost
Order processing costs refer to the costs you incur when processing an order. This cost will include materials used, any overheads and labour expenses. Tracking metrics like this allows you to identify opportunities to save money down the line while helping you improve your financial efficiency and profitability.
To measure this metric, sum up the costs associated with processing your orders and divide it by the total number of orders processed. Implement tracking by using accounting and inventory management systems to log all relevant costs. Regularly review this data to identify trends and areas where costs can be reduced, helping you optimise order processing and increase profitability.
Cost per line item shipped
This refers to the expense associated with shipping each line item. It’s important as it allows you to assess how efficient you are at shipping goods while helping you to optimise your logistics moving forward. This can lead to significant savings.
To measure this metric, sum up your shipping costs and divide them by the total number of line items shipped. Implement tracking by using accounting and shipping management systems to log all shipping expenses. Regularly review this data to identify areas for cost reduction and improve shipping processes, ultimately enhancing your overall logistics efficiency.
Storage cost per unit
Storage cost per unit refers to the cost of storing each unit within your warehouse. Optimising space utilisation helps to reduce holding costs, and it also ensures a lean inventory that’s both cost-effective and efficient.
To calculate this metric, take the total cost of storage and divide it by the number of units you’re holding. Implement tracking by using inventory and financial management systems to log storage costs and unit counts. Regularly review this data to identify opportunities for space optimisation and cost reduction, helping to maintain an efficient and cost-effective storage system.
Labour cost per order
This helps you to detail the cost of labour for processing each order. Evaluating workforce efficiency helps you to identify areas for cost reduction while enhancing operational efficiency as a whole.
To calculate this metric, add your total labour costs and divide them by the number of orders processed. Implement tracking by using time-tracking and payroll systems to log labour hours and costs associated with order processing. Regularly review this data to pinpoint inefficiencies and make adjustments to improve productivity and reduce labour costs per order.
Return processing cost
Return processing cost shows how much it costs you to handle returned items. This metric is crucial as it helps you manage expenses for reverse logistics while giving you the chance to improve your return policy. This can lead to improved customer satisfaction, as well as fewer losses.
To calculate this metric, take the total costs incurred by processing returns and divide it by the number of returned items. Implement tracking by using accounting and inventory management systems to log return processing costs. Regularly review this data to identify inefficiencies and opportunities for cost reduction, helping to streamline the return process and enhance overall profitability.

KPIs to help monitor warehouse labour productivity
Labour productivity KPIs allow you to identify performance gaps while optimising your workforce across different departments.
Warehouse labor productivity
Warehouse labour productivity refers to employee efficiency. It details the amount of work they’re getting done. A common way to measure this would be units per hour. This metric is important as it reflects the efficiency of your warehouse, which has a direct impact on performance.
To measure this KPI, calculate the number of units processed per hour of labour. Implement tracking by using time-tracking systems and Warehouse Management Systems (WMS) to log hours worked and units processed. Regularly review this data to identify areas for improvement and optimise workflows, enhancing overall labour productivity and warehouse efficiency.
Cycle count accuracy
This is the accuracy of cycle counts when compared to system records. This is done during periodic inventory audits. It’s important as it helps to ensure ongoing accuracy regarding existing inventory. It also reduces the need to do a full physical count, which can be time-consuming.
To measure this KPI, compare your cycle count to your inventory record and calculate the accuracy percentage. Implement tracking by conducting regular cycle counts and using a Warehouse Management System (WMS) to log discrepancies. Regularly review this data to identify patterns and improve counting processes, maintaining high inventory accuracy and operational efficiency.
Warehouse capacity utilisation
Warehouse capacity utilisation refers to the warehouse space that’s being used, in comparison to the available space available. This metric is important as it maximises storage efficiency while helping you to reduce the overhead costs associated with space that’s not being used.
To measure this KPI, divide your used space by the total space available and multiply by 100 to get the utilisation percentage. Implement tracking by regularly assessing space usage and using a Warehouse Management System (WMS) to log these figures. Regularly review this data to identify opportunities for optimising space utilisation, ensuring efficient use of your warehouse capacity.

KPIs to help monitor warehouse safety
Warehouse safety KPIs are useful for ensuring that your team has a safe working environment. It also helps to reduce the amount of downtime, due to workplace accidents.
Safety incident rate
Safety incident rates refer to the number of incidents, including accidents and near-misses, in relation to the number of hours that are being worked. Metrics like this are important to track, as it helps you to provide a safe working environment while reducing downtime. Employee morale can also be improved by taking note of your current safety incident rate.
To measure this metric, track the number of incidents over a set period, divide this by the total hours worked, and then multiply by a standard factor (e.g., 200,000 for incidents per 200,000 hours worked). Implement tracking by using safety management systems to log incidents and hours worked. Regularly review this data to identify trends and implement safety improvements, maintaining a safe and efficient workplace.
Lost time injury frequency rate (LTIFR)
This is the number of lost time injuries you have, per million hours worked. This is important as it measures the impact of each workplace injury, and its impact on your team’s safety. Lower LTIFR rates indicate that you have a safe working environment, whereas higher rates show that you need to make further improvements.
To measure this, divide the number of lost time injuries by the total hours worked, then multiply by 1,000,000. For example, if you have 3 lost time injuries and 500,000 hours worked, your LTIFR rate would be 6. Implement tracking by using safety management systems to log lost time injuries and hours worked. Regularly review this data to identify safety issues and implement measures to reduce injury rates, ensuring a safer workplace.
Accidents per year
This is the number of accidents that occur within your warehouse, every year. Tracking this metric is imperative, as it gives you a clear overview of how safe your warehouse is. If you have a high number of accidents, this can indicate that you need to improve your safety measures.
To measure this KPI, record the number of reported accidents within a year and compare them to your historical records. Implement tracking by using safety management systems to log all accidents. Regularly review this data to identify trends and areas for safety improvements, helping to create a safer work environment and reduce the number of accidents over time.
Time since last accident
Time since the last accident is the number of days, weeks or months it has been since the last accident in your warehouse occurred. Measuring this is important as if you can go a longer period without an accident, this can lead to a safer working environment.
To measure this, track the date of the last accident and calculate the elapsed time since then. Display this KPI within the warehouse to promote safety awareness and encourage a culture of safety among employees. Regularly updating and reviewing this metric can help maintain focus on safety and further reduce the likelihood of accidents.
How StoreFeeder can save you the work
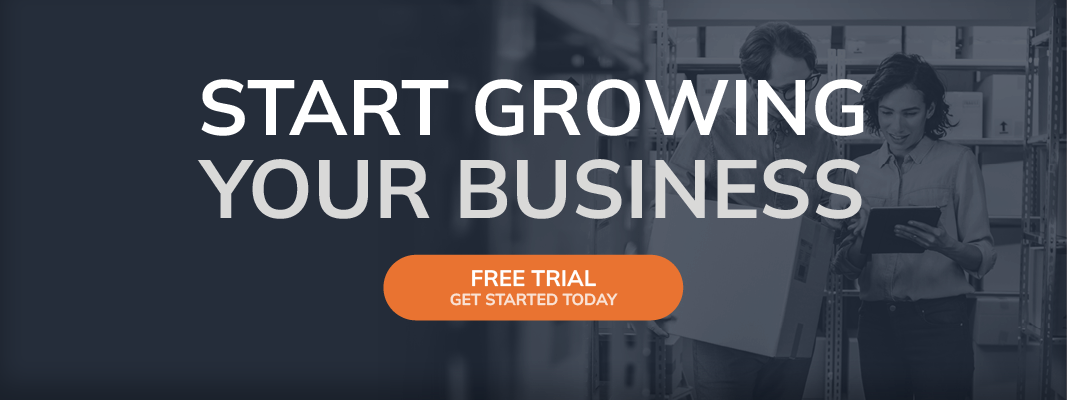
StoreFeeder can support your warehouse operation by measuring the above KPIs so you can optimise your operation for both efficiency and profitability. StoreFeeder has numerous app-based features, including picking functions. This ensures that the right products are picked by your team, leading to higher customer satisfaction rates.
With automated processes, including inventory management and shipping updates, it’s also easier to manage stock across multiple websites and marketplaces. Features like this can lead to significant improvements in cost savings and productivity, enhancing customer satisfaction while improving operational efficiency.
Other features of the StoreFeeder warehouse management system include support for multiple currencies, Spotify integration, barcode scanning, serial number tracking and business metric tracking support. If you want to learn more, book a demo and register for a trial. We’re confident you’ll be able to see a huge improvement in your operation while having a whole new level of control over your business.
Conclusion
Efficiently managing a warehouse is critical for any organisation, and understanding the right KPIs is essential for achieving this goal. From order accuracy to labour productivity, tracking these KPIs helps identify areas for improvement, ensuring your warehouse operates smoothly and efficiently.
By focusing on key metrics such as inventory accuracy, order lead time, and safety incident rates, you can address potential issues before they escalate, leading to increased customer satisfaction and reduced operational costs. Implementing a comprehensive Warehouse Management System (WMS) like StoreFeeder can simplify this process, providing automated tracking and insights that enhance overall performance.