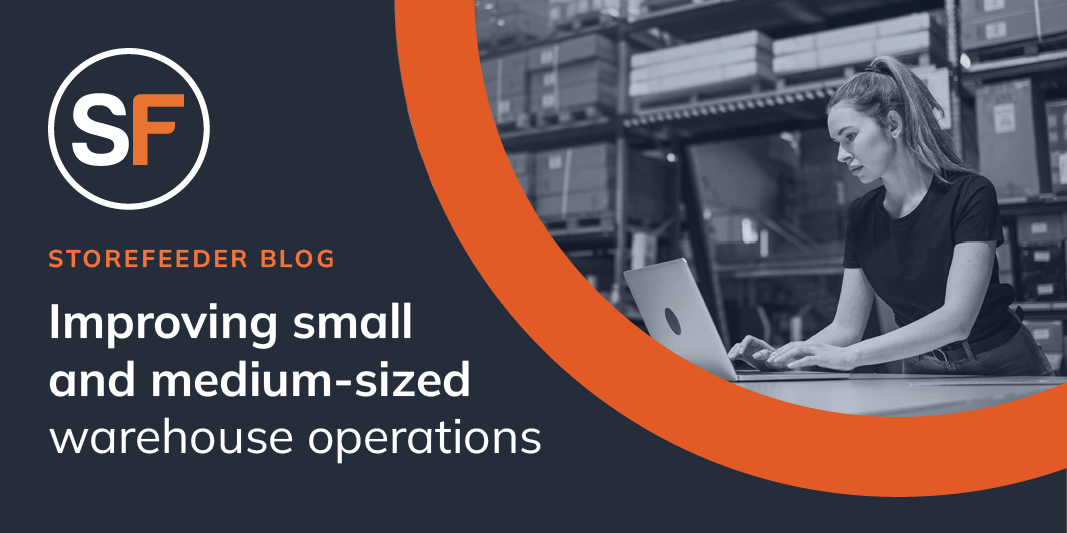
Improving small and medium-sized warehouse operations | StoreFeeder
July 12, 2024
Warehouse operations are an essential feature for small and medium-sized businesses across multiple industries. Unfortunately, though, many companies struggle with operational efficiency in the environment due to limited space and resources.
While the UK’s warehousing industry was valued at £78.8 billion in 2022 and continues to grow, increased expectations largely attributed to the growth of eCommerce omni-channel retail have placed huge pressure on warehouse managers as they look to optimise space, manage inventory, and ensure timely deliveries without sacrificing cost-effectiveness.
The consequences of inefficient warehouse operations include financial losses, reduced productivity, inventory problems, and delays in fulfilment. Thankfully, though, small and medium-sized businesses can significantly boost warehouse efficiency by following best practices and developing a clear strategic approach.
In this guide, we’ll uncover some of the top tips to level up your warehouse operations, so let’s get started.
The importance of optimising warehouse operations
There are now over 5,000 warehouse businesses operating in the UK - and failing to keep pace with a rapidly evolving industry will see your venture fall behind. Improving warehouse operations in small and medium-sized businesses will help reduce costs, boost customer satisfaction levels, and give the company a competitive edge.
Small and medium businesses face several challenges in this field including limited space, budget constraints, fluctuating order volumes, and the need for scalable systems. However, streamlined operations can yield a host of benefits including but not limited to:
● Faster order fulfilment, which is vital as 60% of consumers now expect their delivery to arrive within 48 hours.
● Improved inventory management, ensuring that you avoid issues with your stock or the equipment used for warehouse duties.
● Better space utilisation, with a view to beating the average 85% peak space utilisation figures shown in the industry.
● Increased profitability, which facilitates sustained success and opens the door to potential expansion.
While the rewards are clear, the thought of overhauling your warehouse operations is very daunting. Thankfully, these small changes can significantly enhance warehouse efficiency. Better still, by focusing on incremental improvements, you can transform your business without feeling overwhelmed or causing disruption.
How you can improve operations in your warehouse
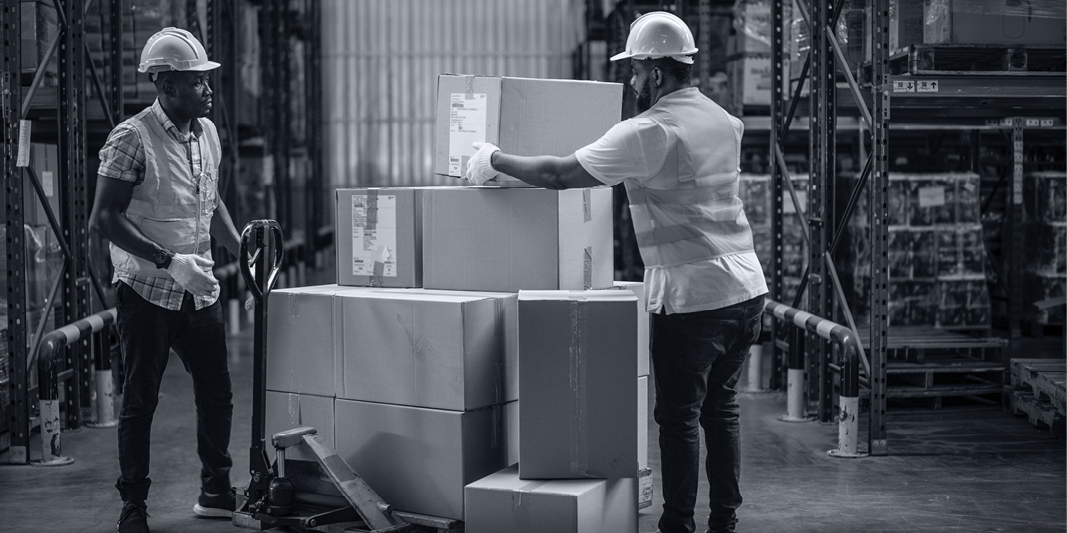
Improve inventory management
Inventory management is an integral feature of any efficient warehouse. With the right practices in place, speed and accuracy can see significant improvements while simultaneously ensuring that all warehouse operators are on the same page. Here’s how to improve yours.
Ensure accurate inventory tracking
Introducing a multi-channel inventory management system (IMS) to monitor stock levels, locations, and movements with real-time tracking capabilities will transform warehouse operations with incredible results.
Inventory management tools can prevent stockouts, reduce overstocking, and guarantee inventory accuracy at all times. In addition to boosting daily warehouse efficiency, this warehouse technology will alert you to any issues that surface thus allowing you to find a quick resolution.
To make the most of your IMS and inventory tracking efforts, you should:
● Use barcode scanning or RFID to automate data entry and minimise errors.
● Regularly update inventory records and reconcile them with physical counts.
● Integrate your IMS with other business systems (e.g., ERP, eCommerce platforms) for seamless data flow.
Implement ABC analysis
Good organisation is a key aspect of efficient warehouse management. ABC analysis is the ideal solution for improved warehouse efficiency. It revolves around categorising inventory into three item groups:
● A (high-value, low-quantity)
● B (moderate value and quantity)
● C (low-value, high-quantity)
It focuses management efforts on the most critical inventory, optimising resource allocation with optimal efficiency. For example, it can highlight the 20% of inventory that drives success as per Pareto's 80/20 rule. Above all else, it removes guesswork and doubt.
When implementing ABC analysis, you should be sure to:
● Review and adjust ABC classifications regularly based on sales data and market trends.
● Apply stricter controls and more frequent audits to A items, while simplifying management for B and C items.
● Use this analysis to inform purchasing decisions and reduce holding costs.
Carry out regular audits and cycle counts
Inventory audits and cycle counts will also help improve inventory management by maintaining accurate stock records. Crucially, it highlights discrepancies at the earliest opportunity. In turn, this reduces large-scale inventory audits and maintains data integrity.
Given that inventory discrepancies played a key role in Asos’s 68% drop in annual profits back in 2019, small and medium-sized businesses must learn from this situation to avoid suffering a similarly damaging episode. Using regular audits to maintain warehouse efficiency and address any issues quickly will certainly help.
To unlock the best results, it’s important to:
● Schedule cycle counts for different product categories at varying frequencies based on their importance and turnover rates.
● Use technology like mobile counting apps to streamline the counting process and update records instantly.
● Train staff to perform counts during low-activity periods to minimise disruptions.
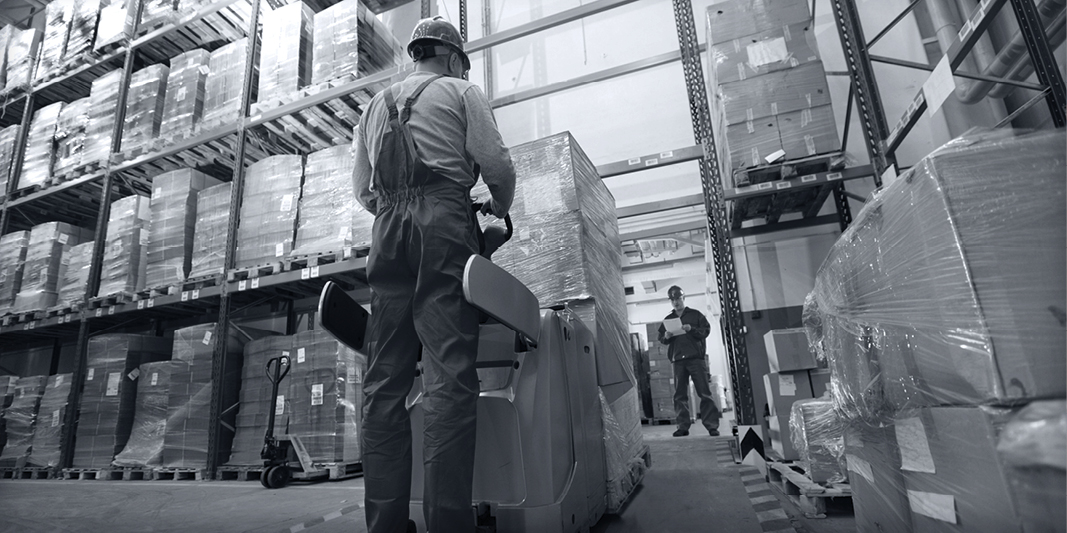
Maximise space utilisation
Space utilisation is an area of warehouse efficiency where most small and medium-sized businesses can make a huge improvement with very simple adjustments. When you do, it will provide the perfect foundation for running an optimised warehouse to unlock a better use of time, money, and resources.
Optimise your warehouse layout
The warehouse layout covers the receiving area, storage area, packing area, shipping area, and service area. Ultimately, your goal should be to design a layout that minimises travel time, optimises storage, and facilitates efficient workflows.
Getting this right Improves picking and packing efficiency and reduces operational costs, while also enhancing space utilisation. Picking accounts for up to 55% of warehouse operational expenditure, so the layout should reflect this if you want to unlock positive results for the business.
Additional steps to consider when redesigning the warehouse layout are:
● Place high-turnover items close to shipping areas to reduce travel time.
● Use cross-aisle locations for frequently picked items to streamline access.
● Create dedicated areas for receiving, storage, picking, packing, and shipping to maintain a smooth flow of operations.
Implement vertical storage solutions
You can’t change the floorspace of your warehouse unless you make an extension. Thankfully, vertical storage systems like shelving, pallet racks, or mezzanines will make a huge difference by utilising warehouse height more effectively.
The changing commerce landscape has seen the development of warehouses with at least one million square feet grow by 345% in recent years. Small and medium-sized businesses might not be able to match this, but they can increase their storage capacity without expanding the warehouse footprint through vertical storage.
For the best results, warehouse managers must look to:
● Use adjustable shelving to accommodate different product sizes and optimise space.
● Install safety features like guardrails and safety netting on mezzanines to prevent accidents.
● Label shelves clearly to facilitate quick identification and retrieval of items.
Adopt lean inventory practices
Adopting lean practices to minimise waste, streamline processes, and maintain optimal inventory levels will go a long way to maximising space utilisation. It reduces excess stock, enhances organisation, and improves overall operational efficiency.
Lean management aids all industries “through a proven process of visualisation, organisation and standardisation”. In warehouses, it ultimately saves the business time and money while also boosting accuracy throughout daily operations. By trimming the fat, teams are free to work efficiently and effectively.
The following tips should help you achieve the desired results:
● Implement Just-In-Time (JIT) inventory practices to reduce holding costs and align stock levels with demand.
● Use Kanban systems to signal when stock needs replenishing, avoiding overstocking.
● Regularly review inventory levels and adjust purchasing practices to match sales trends.
Adopt technology for improved efficiency
Understandably, warehouse technology will play a key role in adapting the warehouse environment so that it can reflect the current landscape. Not all tech additions are worthwhile, but the best items will unlock increased speed, accuracy, and profitability. Conversely, persisting with outdated options would cost you dearly.
Inventory Management Systems (IMS)
When thinking about inventory management, finding the right IMS package to automate inventory tracking, manage orders, and streamline warehouse operations is key. The latest tools enhance accuracy, reduce manual workload, and provide valuable data insights with reliability in mind.
The right IMS software will directly improve warehouse operations while also delivering clearly presented info to help employees make data-driven decisions. Likewise, Software as a Service (SaaS) solutions can evolve over time to reflect tech updates and business expansions.
When adding an inventory management system, you should be sure to:
● Choose an IMS that integrates seamlessly with your existing systems and scales with your business.
● Use cloud-based IMS solutions for real-time access and updates, regardless of location.
● Regularly update the system to take advantage of new features and improvements.
Barcode and RFID
Barcode scanning and RFID systems are an ideal way to boost warehouse efficiency as all data is recorded with real-time results. This improves inventory tracking, reduces errors, and speeds up daily processes with immediate benefits for your inventory management.
Stock control is simplified when pallets and other items are accounted for with optimal accuracy and minimal effort from your employees. With the RFID market currently showing a compound annual growth rate of over 11%, now is the time for warehouse managers to embrace this superior solution for their businesses.
Using this warehouse technology to enhance the venture is at its best when you:
● Label all inventory items and storage locations with barcodes or RFID tags for quick identification.
● Equip staff with handheld scanners to facilitate fast and accurate data capture.
● Integrate barcode/RFID technology with your IMS to automate updates and improve visibility.
Warehouse Management Systems (WMS)
A dedicated WMS is used to coordinate and optimise warehouse activities ranging from receiving to shipping, covering all tasks throughout the warehouse cycle. As well as increasing operational efficiency and reducing errors, this technology supports scalable growth.
It's one of the most effective ways to maximise productivity, minimise costs, and meet growing customer demands as it will optimise all ongoing planning and management duties. In turn, daily operations will run far more smoothly while related issues like space utilisation are indirectly supported too.
For the best results, warehouse managers should:
● Look for WMS solutions that offer features like pick path optimisation and automated task assignment.
● Use WMS analytics to identify bottlenecks and inefficiencies in your processes.
● Train staff thoroughly on using the WMS to ensure they can leverage its full capabilities.
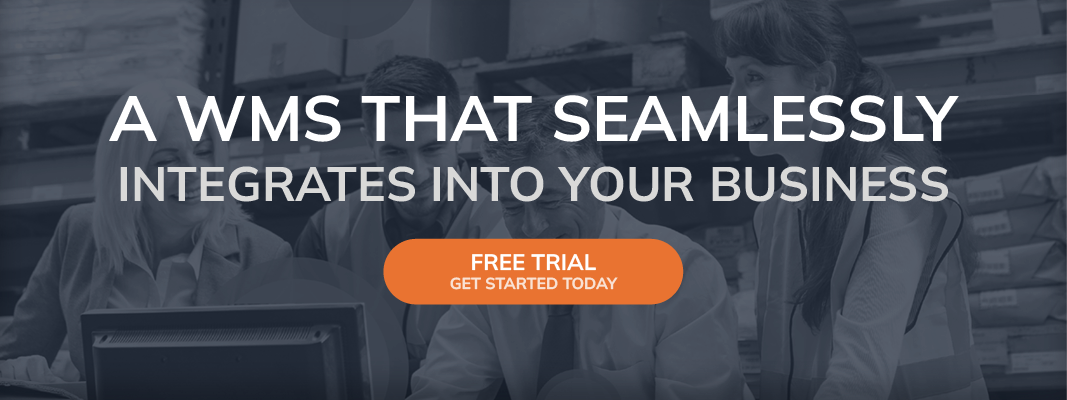
Ensure your staff are working efficiently
Employees are the company’s greatest asset in any environment, and warehouses are no different. Small and medium-sized businesses can transform their entire operation by investing in simple steps to improve individual and collective productivity. Better still, it’ll lay the foundation for easy onboarding when the company expands.
Implement Standard Operating Procedures (SOPs)
Developing Standard Operating Procedures (SOPs) for all warehouse processes is an ideal starting point that promotes consistency and efficiency with instant results. As well as providing clear direction to individuals and teams alike, it makes it far easier for managers to identify and address problems.
SOPs reduce errors, shorten training time for new employees, and improve overall process reliability. Meanwhile, 34% of employees have to guess their priorities at work. This is a fantastic way to overcome this issue.
When implementing SOPs, it’s important to:
● Document each step of key processes, such as receiving, picking, packing, and shipping.
● Review and update SOPs regularly to reflect changes in operations or technology.
● Use visual aids, such as diagrams or videos, to enhance the clarity and effectiveness of SOPs.
Cross-train employees
Cross-training employees to perform multiple roles and tasks within the warehouse is another potential game-changer for the business. It provides operational flexibility, increases workforce productivity, and improves response to fluctuating workloads. Meanwhile, it ensures that all employees understand the perspectives of their colleagues.
Research shows that 74% of workers are happy to cross-train as it keeps them employable. It can also make their jobs more engaging, which leads to increased productivity and fewer mistakes. A stronger workforce will lead to improved warehouse operations.
To get the best out of all warehouse employees, you must:
● Develop a cross-training program that includes key tasks and functions across the warehouse.
● Rotate employees through different roles to maintain skills and avoid monotony.
● Encourage knowledge sharing among employees to foster a versatile and adaptable workforce.
Implement lean warehousing techniques
Implementing lean warehouse techniques will focus on developing the right tactics and using the ideal warehouse technology to unlock increased efficiency. This could mean automating manual processes or completing additional steps to eliminate waste, streamline processes, and improve general workflows.
Lean warehousing increases efficiency, reduces costs, and enhances overall productivity while also opening the door to smoother expansions. It's suggested that this approach can generate a 40% saving on inventory while ensuring that deliveries are fast and correct.
Some of the top tips for implementing the right techniques are to:
● Identify and eliminate non-value-added activities in your processes to streamline operations.
● Use 5S principles (Sort, Set in order, Shine, Standardise, Sustain) to organise and maintain the warehouse.
● Continuously seek input from employees on ways to improve processes and reduce waste.
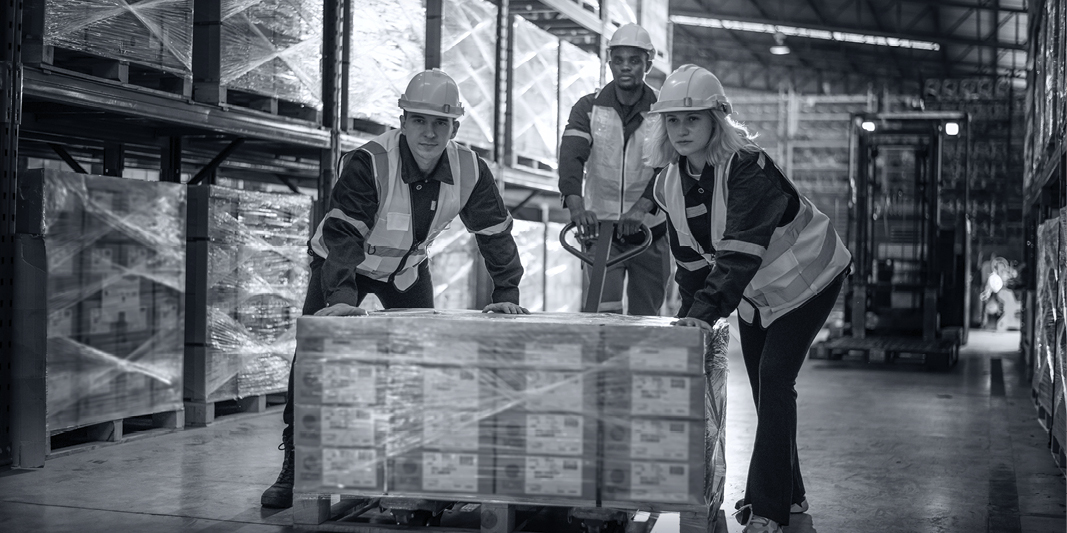
Invest in staff training and development
Staff training and development isn’t only about cross-training. Warehouse managers must also look to invest in the continued progress of employees relating to their primary responsibilities. In turn, this can give the company a competitive edge by keeping pace with the latest industry changes. Here’s how to do it well.
Offer continuous training programs
Ongoing training keeps all staff updated on best practices, new technologies, and operational procedures. It enhances skills and ensures effective use of tools and systems. Employees will be empowered and capable of producing more.
As well as improving daily operations, regular training keeps employees motivated. Happy employees are 13% more productive while they also become less likely to leave their job. Achieving a lower staff turnover rate can only have a positive impact for the warehouse’s overall efficiency and consistency.
To stay on top of training programs, warehouse managers should:
● Schedule regular training sessions and refresher courses to keep skills current.
● Use a variety of training methods, including hands-on practice, e-learning, and workshops.
● Encourage feedback from employees to improve training programs and address knowledge gaps.
Ensure safety and ergonomics training
The warehousing industry is one of the worst for non-fatal injuries. For small and medium-sized businesses, regular training is a vital feature for avoiding downtime, legal issues, and damaged reputations. Not to mention the impact it has on order fulfilment.
Safety and ergonomics training can prevent injuries and promote a healthy work environment while also reducing accident rates, lowering absenteeism, and increasing job satisfaction. It also ensures that employees handle all tasks, like picking and packing, in the safest and most efficient ways.
To maximise the benefits of safety and ergonomics training, warehouse managers should:
● Provide training on proper lifting techniques, use of equipment, and ergonomic best practices.
● Implement safety drills and regular safety audits to reinforce safe behaviour and identify risks.
● Ensure that workstations and equipment are designed to minimise physical strain and support ergonomic practices.
Offer performance incentives
If you want employees to thrive in the warehouse environment, playing up to their human qualities will be vital. Implementing performance-based incentives to motivate staff and improve productivity is an ideal solution.
It encourages employees to meet or exceed performance targets, leading to better operational outcomes. Furthermore, seeing colleagues get rewarded can inspire employees. Over half of all employees across all sectors, including warehouses, are prepared to do more. So, it can provide a quick route to improved warehouse operations.
To boost warehouse efficiency through employee incentives, you can:
● Offer rewards for achieving key performance indicators (KPIs) like order accuracy, picking speed, and attendance.
● Create a balanced incentive program that recognizes both individual and team contributions.
● Regularly review and adjust incentive programs to keep them aligned with business goals and employee expectations.
Leveraging data and analytics
We are living in a data-driven era, and it should be used to leverage success in your warehouse operations. Aside from aiding the decision-making process, data lets you act with greater confidence in daily and ongoing tasks. It's one of the most effective uses of warehouse technology, and deserves immediate attention.
Monitor performance metrics and KPIs
Setting key performance indicators (KPIs) and metrics that can be tracked and monitored can have a huge impact on warehouse performance levels. It provides actionable insights, identifies areas for improvement, and supports data-driven decision-making that are aligned with your objectives.
Common KPIs include inventory cost, inventory turnover, backorder rates, lead times, picking accuracy, and receiving accuracy. With the right KPIs selected, your entire warehouse operation will be geared toward efficiency in the areas that matter most.
Before investing in this strategy, you must:
● Define relevant KPIs, such as order accuracy, pick rate, inventory turnover, and cycle time.
● Use dashboards and reports to visualise performance data and identify trends.
● Regularly review KPI performance with your team and set goals for continuous improvement.
Analyse inventory turnover
Inventory turnover is vital for many reasons. It ensures that your stock levels are aligned with customer demands while also preventing issues like holding stock for long periods. By optimising stock levels in this way, you can also take space utilisation to new heights.
By having the right stock levels for all products, you’ll reduce waste and enhance cash flow with immediate results. Once you are in the habit of accurately calculating the demands, streamlined processes will come naturally. If nothing else, it will be far easier for you to identify the products that you should market more heavily.
Analysing inventory turnover is made easy when you:
● Calculate inventory turnover ratios to assess the efficiency of stock management.
● Identify slow-moving inventory and develop strategies to clear excess stock.
● Use turnover data to refine purchasing and replenishment practices, ensuring alignment with sales trends.
Use forecasting to help plan inventory demand
Data isn't only great for analysing and modifying performances. It can also guide your next steps through accurate forecasting. When done well, you can predict customer demand and plan inventory accordingly. This will naturally ensure that your stock levels and warehouse space utilisation is under control.
Predictive data can improve order fulfilment, reduce excess inventory, and align your supply levels with customer needs. Over half of all customers experience the frustration of items being out of stock. Your business can avoid this and unlock its potential through forecasts.
When using forecasting, you should:
● Use historical sales data and market trends to inform demand forecasts.
● Adjust forecasts regularly based on seasonality, promotions, and other factors.
● Collaborate with suppliers and customers to share information and improve demand planning accuracy.
How StoreFeeder can help improve your warehousing operations
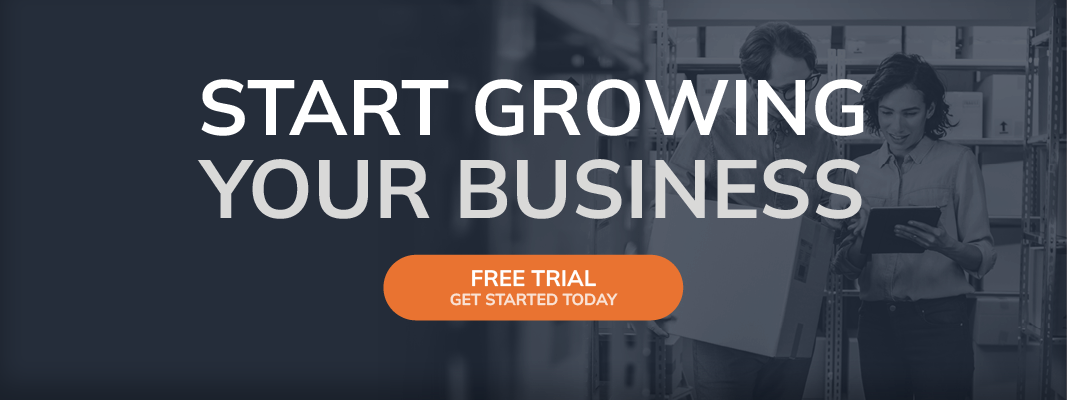
Improved warehouse operations are a major breakthrough for small and medium-sized businesses. By now, you should have a clear understanding of the tactics that could transform your approach. More importantly, you should see that the right warehouse technology sits at the heart of everything. StoreFeeder is the perfect solution that can optimise your eCommerce operations.
StoreFeeder’s advanced inventory management capabilities can streamline processes to unlock increased speed and efficiency. Meanwhile, data analytics provide the insight needed to guide your next moves. In turn, it can be the catalyst for increased productivity and cost savings while also maximising customer satisfaction.
To learn more about what StoreFeeder can do for your business, book a demo today.