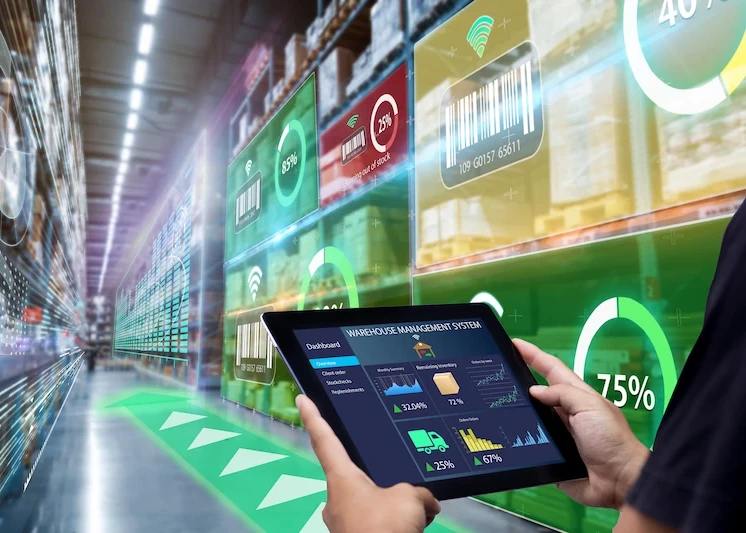
The importance of automation processes within StoreFeeder WMS
February 1, 2024
Introduction:
Warehouse managers understand the critical importance of efficiency and accuracy in their daily operations. As the demands on modern warehouses continue to grow, the need for advanced Warehouse Management System (WMS) solutions becomes paramount.
Part of the advantage of a WMS is the automation functionalities designed to streamline processes and elevate warehouse performance.
In this blog, we go through some of the automation processes within the StoreFeeder WMS and how they can offer your business real benefits.
What is automation in a WMS?
Automations are behind-the-scenes processes that are running 24/7 and designed to save you significant time and help make your day more productive.
Automated processes within the WMS are designed to take the manual decision making, and/or labour from a task that occurs regularly.
Below we go through some of the main automated tasks within StoreFeeder WMS.
Order import automation:
At the start of your StoreFeeder journey with our implementation team, you will link your sales channels, eBay, Amazon, Shopify etc., to the system.
This link is what allows a lot of the automation to happen.
When a customer places an order on channel, it is imported into the WMS and shown on the orders page.
The linking of all your channels and the automation of this import means all your orders are now in one central location and easy to see and process. No need to log into multiple channels or accounts to see orders.
StoreFeeder WMS provides one central order portal and in turn gives you access to easier reporting, analysis and evaluation of both orders and stock.
Inventory update automation:
Because all your orders from all your channels are now coming into one central system and deducting stock from one central stock holding, our system can now provide accurate stock levels based on sales from all channels.
So, we can now provide each channel with an accurate inventory level that reflects all your sales, not just the ones made on each channel.
You will no longer have to manually update stock levels on multiple channels when you receive a delivery of stock, or update Amazon when you sell an item on eBay for example. Automation of this task takes all that manual processing away and ensures that your stock levels on all channels are live and a true reflection of what is actually on the warehouse shelf.
Another benefit of this is greater stock visibility on all channels. Having 50 units in stock no longer means that you put 10 on eBay, 20 on Amazon, 10 on your website etc. The automation of inventory updates means that all 50 can safely be advertised on all channels as each sale is reflected inside StoreFeeder and subsequently pushed to channel to reflect the new stock level on the shelf.
Shipping rules:
Say goodbye to deciding which shipping method each order should have. With shipping rules, or automated courier allocation, you build up a set of pre-determined rules that determine which shipping company and service should be used in different scenarios.
You can base rules on weight, destination, value, size, order channel, and many other criteria. Building up a series of detailed shipping rules means that when an order is imported, our automation allocates the correct shipping company and service to that order straight away.
No more decisions made by warehouse staff on shipping, that could cost you more for deliveries than it should.
Automation takes the human element out of the decision making process.
Stock allocation automation:
With StoreFeeder WMS, we know where your stock is within your warehouse, so when you come to pick the orders, not only will the system decide where you should pick it from, but it will also ensure that the picker walks the most efficient route around the warehouse to pick all the items required.
This automation has real benefits with efficiency within the picking process.
Barcode scanning and despatch automation:
StoreFeeder WMS supports barcode scanning at the despatch stage of the order fulfilment process. This provides an extra layer of automation and accuracy and removes the need for human actions in matching specific items to specific orders.
Simply scan the item and the correct shipping label will print.
Automation at this stage in the process gives warehouse managers confidence, through the reduction in manual data entry errors and mistakes when manually matching products to orders, and only serves to enhance the despatching of orders.
Further to this, once the order is despatched and the label produced, automation again kicks in to send this despatch notification to the sales channel to mark the order as shipped and update the courier, service and tracking number as per the requirements of the sales channel.
Another time saving automation that also removes risk of incorrect information being updated, as could happen if this was done manually on channel.
Conclusion:
StoreFeeder WMS is more than just a software solution; it's a powerful ally for warehouse managers seeking to thrive in today's competitive landscape.
By leveraging its automation functionalities, warehouses can achieve higher levels of efficiency, accuracy, and customer satisfaction and as the demands on warehouses continue to evolve, StoreFeeder WMS remains at the forefront, with automation designed to minimise human interaction in the fulfilment process, providing a reliable and innovative solution to meet the challenges of modern warehouse management.
For more information visit our website
Book a demo or sign up for a free trial and experience how teh automation inherent in the StoreFeeder WMS can offer your business real time benefits,.