
8 Order picking strategies for warehouses | StoreFeeder
July 4, 2024
No matter the size of the warehouse you manage, refining your order picking strategy is key to your success in numerous tasks, from productivity and accuracy, to customer satisfaction and cost management. After all, studies have found that “order packing contributes to more than 55% of the total warehouse cost.”
In a time when businesses are closing rapidly, this is a task that you simply must get right moving forward.
Fortunately, there are numerous different order picking strategies can be employed depending on your warehouse’s layout, product time, and order volume.
In this article, we’ll explore the 8 most common types of warehouse order picking strategies, from single order picking to hybrid picking strategies. By understanding the benefits of each method, you’ll be able to determine which is best for your business.
1. Single Order Picking.
Single Order Picking, also known as discrete picking, is the process of picking items for an order one at a time, typically as the orders come in. Each item is picked individually from start to finish by a single picker, allowing for a simple picking process.
Generally speaking, this strategy is best for smaller warehouses that experience lower volumes of orders. Otherwise, this labour-intensive process can quickly become overly time-consuming, leading to significant delays and opening the door to mistakes. In short, it is simply not the most efficient process when dealing with a high volume of orders.
That being said, there are many benefits associated with this order picking strategy. For example, it's relatively straightforward and easy to implement into your business practices, even when training new staff. This reduces the chances of you dealing with order mix-up errors, improving customer satisfaction rates.
Example Scenario.
An online bookseller receives an order for a single book. The picker retrieves this book from the relevant shelf or SKU and proceeds to the packing area so that the order can be distributed as quickly as possible.
2. Batch Picking.

Batch picking is the process of picking multiple orders simultaneously in batches. In this scenario, a single picker will select items from across multiple different orders in one trip, reducing travel time and maximising picking efficiency while doing so.
This is particularly beneficial in warehouses that receive a high number of orders or when multiple orders containing similar items are placed.
There are many pros associated with this methodology. After all, it means that pickers do not need to go back and forth when packing multiple orders, reducing travel time and allowing them to work more efficiently. This often means that orders are picked (and sent out) much quicker.
However, if this operation is not managed effectively, such as through the use of StoreFeeder’s warehouse management system, there will be a higher likelihood of order mix-ups. It may also not be the ideal course of action for time-sensitive orders, as the items will require sorting and separation post-picking rather than being ready to go.
Example Scenario.
A picker working in a grocery warehouse receives multiple orders for similar household items, such as cleaning supplies or canned goods. The picker collects all these items at once before placing them in separate containers to avoid mix-ups.
3. Wave Picking.
Wave picking is a variation of batch picking, but in this scenario, orders are picked in “waves” based on specific criteria, such as shipping schedules, delivery routes, and order types.
This strategy is the best for warehouses with complex shipping schedules or time-sensitive orders, as it allows pickers to prioritise urgent orders above all others. Efficiency in this regard will allow you to remain ahead of the game, even during busier periods.
That being said, if the waves are not well-managed or synchronised (i.e., orders are not picked ahead of a time-sensitive delivery date), it can lead to numerous bottlenecks that are hard to overcome.
Example Scenario.
A distribution centre for a popular clothing retailer can use wave picking strategies to ensure time-sensitive orders (such as next-day delivery purchases) are ready when delivery trucks arrive.
Waves may be timed so that all products required for their respective delivery truck are picked shortly before it arrives.
4. Cluster Picking.

Cluster picking, sometimes called multi-order picking, is comparable to batch picking. However, items are immediately placed into separate containers during the picking process. This eliminates the need to re-sort the items after the packing process is complete, saving time and energy.
This strategy is best for warehouses that receive moderate to high order volumes, or orders that contain a wide variety of different items. There are many pros associated with this method, especially when it comes to managing an employee's workload. Not only does it reduce the need to re-sort orders, it also reduces travel time.
The biggest challenge associated with this challenge is that pickers must be able to manage large numbers of orders simultaneously without making any mistakes. This means that careful monitoring is required.
Example Scenario.
A cosmetic warehouse could use a cluster picking strategy to ensure that as many orders as possible can be sent out at once. Each order is picked simultaneously, with items being placed into a bin or cart that corresponds with the specific order.
5. Zone Picking.
Zone picking requires warehouse managers to divide warehouses into distinct zones and assign each picker a zone to work within. When an order is placed, pickers within the relevant zones will select items and consolidate them at a central point.
This strategy is generally best within larger warehouses, especially those that have a diverse inventory, such as an electronics warehouse. This is because it does not require pickers to traverse the entire warehouse to find items, speeding up the process quite considerably.
Again, this is a methodology that requires a high level of planning to reap the most benefits. For example, each zone must be managed efficiently to ensure an equal distribution of work among pickers, with the most efficient or effective pickers being placed in the higher-demand spaces.
Example Scenario.
An electronic product distribution warehouse can be divided into multiple zones to maximise efficiency when picking orders. For example, the space can be divided into sub-sections such as gadgets, large appliances and accessories. Pickers in each zone are in charge of collecting items when orders come in and taking them to a central point for shipping and delivery.
6. Pick-to-Box

Pick-to-box is a strategy that requires the order pickers to place items directly into shipping boxes or containers. For this reason, it is also known as cartonisation. Again, this can be a great way to streamline the picking process, as repacking is not necessary. Orders are ready to go as soon as they have been picked.
This method works perfectly for businesses looking to fulfil small to medium-sized orders, as individually picking and packing each item for large volumes of orders could quickly become laborious. Pickers must also be able to select the correct form of packing (i.e., box sizes) and quantities to prevent wastage or items being damaged in transit.
Example Scenario.
An online pet supply company requires their fulfilment centre to carry out pick-to-box picking on all customer orders. This means that multiple products can be placed into a single box, whether they’ve ordered toys, accessories, or pet food.
7. Automated Picking Systems.
As the name suggests, automated picking systems rely on the implementation of advanced technology, such as robots, conveyors, and automated storage and retrieval systems (AS/RS), to pick items. This reduces (or eliminates) the need for human intervention, making for a more efficient and often much quicker picking process.
This is best applied in high-volume warehouses with a wide range of SKUs, as it allows for orders to be shipped and picked as efficiently and seamlessly as possible. It's a great way for business managers to reduce overheads in the form of labour, hiring, and training costs.
Of course, a significant investment is also required to implement this technology in a warehouse. These systems also require constant maintenance to keep things running smoothly.
Example Scenario.
Many eCommerce giants use automated picking robots, which are programmed to quickly navigate through the warehouse, retrieve items from shelves, and deliver them to package stations.
8. Hybrid Picking Strategies.
Hybrid picking strategies involve using a mixture of the strategies outlined above to create a highly customised approach to picking that meets the unique needs of your business or operations. For example, while you may be keen to implement the picking technologies listed above, you can also have employees on-site to carry out single-order picking tasks.
This is a more flexible approach to order picking that allows you to react to changing order volumes, especially during busier/quieter periods. This means that everything from efficiency to productivity can be heightened, regardless of the kind of orders you're dealing with.
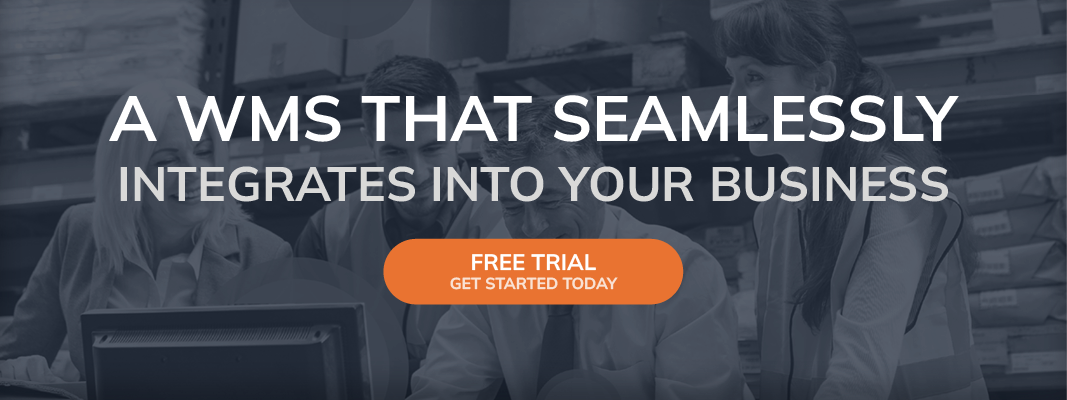
How To Order Picks In A Warehouse.
Knowing how to properly order picks in a warehouse environment can help business owners maximise efficiency, productivity, and customer satisfaction rates.
It's important to investigate inventory rotation methods that enable you to manage the flow of goods effectively. This allows you to take a wide variety of factors into account, from product shelf-life to your overall inventory management goals.
There are four primary methods of inventory rotation:
● FIFO (First in, First Out)
● LIFO (Last in, First Out)
● FEFO (First Expired, First Out)
● LSFO (Last Sold, First Out)
1. FIFO.
As the name suggests, the “first in, first out” method means that the oldest inventory (the first items received) is picked and despatched ahead of newer inventory. This is a method that is typically used when handling items with a limited shelf-life, such as food or pharmaceuticals. When implemented strategically, this method can reduce waste as it ensures products are sent out far in advance of their expiry or use-by date. It also simplifies the process of inventory tracking, especially when picking software is used.
This method requires warehouse managers to be incredibly organised so that the rotation of products is well-managed. It may also require businesses to rearrange their warehouse to ensure employees can quickly access older stock.
This methodology is best utilised alongside single order picking, batch picking or zone-picking strategies.

2. LIFO.
Last in, first out means that the most recently received items are picked and shipped first. This strategy is not as popular as others, but that does not mean it is without its benefits. For example, as newer stock tends to be stored at the front of most warehouses, this can reduce pickers' travel times. For this reason, it is best suited to non-perishable goods or products that don’t degrade over time, such as electronics.
However, older inventory must still be managed carefully to ensure that these products remain suitable for sale. This methodology is best utilised alongside single order, batch, or zone picking strategies, as it helps make them much more efficient.
3. FEFO.
The first expired, first out methodology can improve warehouse picking by ensuring that products with the nearest expiration date are picked and despatched first, regardless as to when they were received. This is perfect for perishable and time-sensitive goods with varying shelf lives, such as within grocery despatch centres.
This method can also help businesses to ensure that they remain compliant with the relevant product safety laws and regulations, especially when handling perishable items. Finally, it can also reduce waste and improve customer satisfaction rates by ensuring they always receive fresh products.
The only downside of this approach is that it requires meticulous monitoring and tracking. Fortunately, there are tools like StoreFeeder available that can help in this regard, providing you with easy insight into the stock you currently have on-site and the urgency with which it must be despatched.
This methodology is best used alongside single order, batch, or zone picking strategies.
4. LSFO.
Last Sold, First Out is a method that involves picking and despatching the most recently sold items first. This is generally used in industries where the sales order determines the picking sequence, such as online fashion retailers conducting flash sales or offering priority next-day delivery.
This method is a great way to manage customer expectations when it comes to fast and efficient delivery, especially when next-day delivery is promised. However, it could mean that older deliveries are put on the back burner, leading to potential frustrations.
This methodology is best utilised alongside single order, batch or zone picking strategies.
Other specialised methods.
JIT (Just-In-Time) Picking. This practice involves picking items when they are needed for immediate shipment.
Kanban Picking. This practice involves using a visual system to signal when stock needs to be picked or replenished, helping to ensure smooth business operations and avoid stock depletion.
How can StoreFeeder Help?
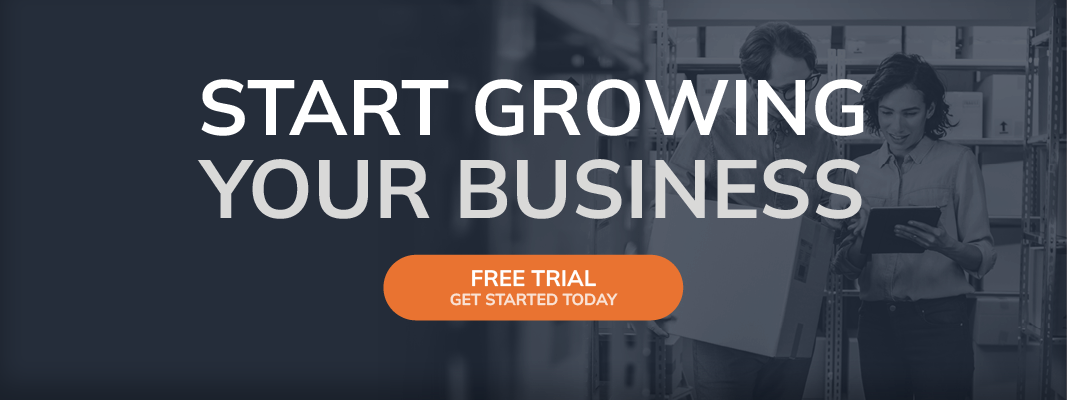
Regardless of which order picking strategy you choose, from consolidated picking to automated picking systems, the team at StoreFeeder are here to help. Our Warehouse Management System (WMS) allows you to closely monitor everything from product inventories to picking speed, so that you’re able to implement changes to your system when necessary.
This not only means that you’re able to run a more efficient warehouse, but it will also help when it comes to growing your business; meaning customers are more likely to recommend your products to others, or place additional orders in the future.
If you’d like to find out more about our time and cost-saving picking software, please don't hesitate to get in touch today!
Conclusion.
In short, choosing the right order picking strategy is key to the long-term success of both your warehouse and your business as a whole. Relying on the wrong strategy can slow down the picking and shipping process, leading to a backlog of orders and plenty of frustrated customers - many of whom will take their money elsewhere in the future.
Conversely, when you’ve selected the right picking strategy for your business, things will work much more smoothly. You’ll notice that orders are picked and processed at a much quicker rate, without any stress or running the risk of product wastage.
As such, now is the perfect time to evaluate your current picking methods so that you can improve your business operations. As mentioned above, our WMS tool can help you improve order-picking efficiency, making it much easier for your team to manage an influx of diverse orders without putting your pickers on the path to burnout.
If you’d like to find out more, please do not hesitate to get in touch today!