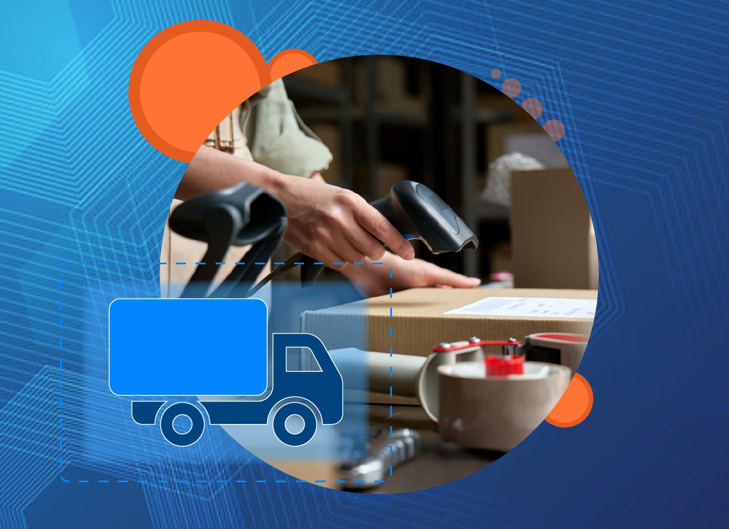
Revolutionise your despatch process with StoreFeeder's barcode packing function
July 1, 2024
Are you tired of dealing with mis-picked orders and endless returns?
Imagine a world where your despatch process is faster, more accurate, and effortlessly efficient.
Well, wait no more, welcome to StoreFeeder's barcode packing function, the game-changing solution your warehouse needs to enhance order processing and delight your customers every single time.
Why is this important?
Efficient and accurate order processing is the lifeline of any successful eCommerce business.
StoreFeeder's barcode packing function is here to revolutionise your despatch stage, ensuring every order is accurate, reducing errors, and cutting down on costly returns.
This innovative tool lets you streamline your workflow with unprecedented speed and precision, making the nightmare of mismatched labels and wrongly products a thing of the past.
How does barcode packing work?
Gone are the days of sorting through orders one by one, with StoreFeeder's product-led despatch, the system guides you through the process with ease.
Once the items for the pickwave are picked, just grab any product from your trolley, scan it, and watch as the system automatically identifies the corresponding order. If no additional items are needed, the system will immediately print the label and despatch the order.
No more manual matching, no more confusion, just scan, pack, and attach the label.
The benefits of barcode packing
So, what are the benefits of StoreFeeder's barcode packing function and how can it transform your order processing?
• Increased accuracy: By scanning barcodes during the packing process, you ensure that each item is correctly picked and assigned to the right order, drastically minimising the risk of errors. Say goodbye to errors and hello to satisfied customers.
• Reduced returns: Labels only print once all correct items are scanned, drastically cutting down the risk of incorrect shipments and the costly returns that follow.
• Improved efficiency: Speed up your packing process. Allowing packers to quickly verify items and removing manual matching processes, moves orders through the despatch stage without delays.
• No product knowledge needed: The system operates using EAN/barcodes, thus eliminating the need for the despatch team to have detailed product knowledge. Simply scan, pack, and attach the label.
Packing with precision
Caught your attention? What is the process for achieving these improvements?
• Enter the pickwave: At the packing station, select 'Scan Products' to access the 'Edit Pickwave' screen. Here all unscanned items will display, highlighted in red.
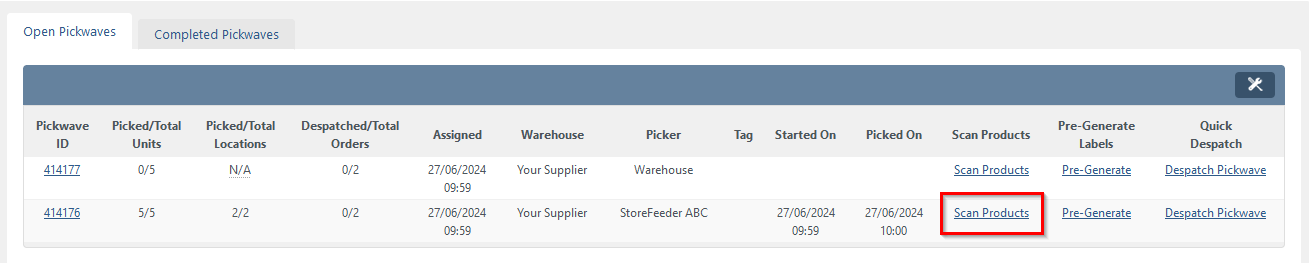
• Scan and pack: Take any item. scan its barcode, and StoreFeeder will automatically select the corresponding order. For single-item orders, the despatch note, and delivery label, are generated immediately.

• Handle multi-item orders: For orders with multiple items, after the initial scan, a new page will pop up showing you which other items you require to complete the allocated order. Then simply select and scan each required item as prompted by the system. Red and amber lines turn green to indicate fully scanned items. Once the order is complete, the label prints, and you’re ready for the next product.
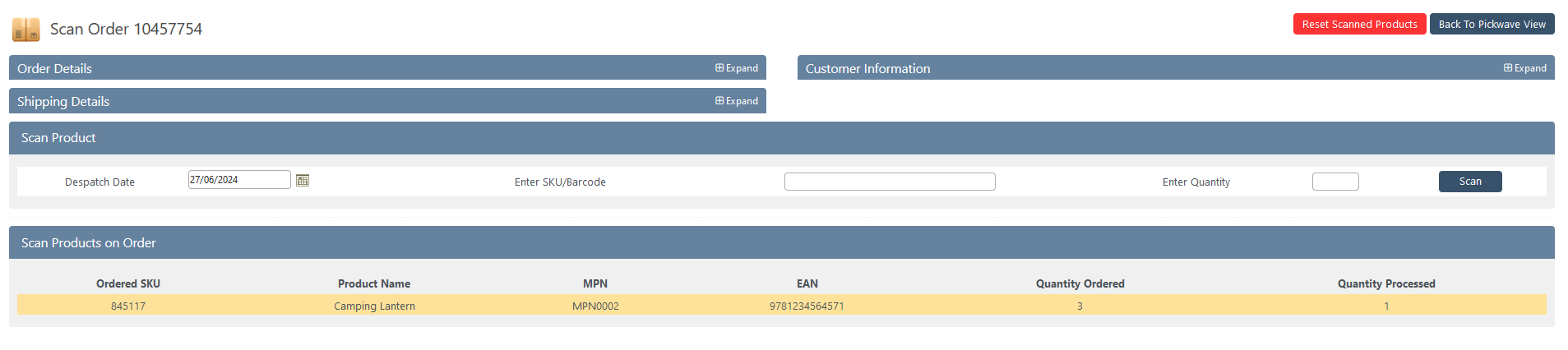
Completing the process
Continue scanning and packing until all orders in the pickwave are processed. At every stage, the system updates each order’s status in real-time, ensuring accurate records and order status information on your sales channels.
The system allows users to monitor progress with colour-coded indicators. Red for unscanned items, amber for partially scanned, and green for fully scanned.
At the end of the pickwave, all lines should be green, and all items should have been scanned, leaving an empty trolley. If there are items left, and all lines are green, too many items have been picked, and likewise if some lines remain red or amber but the trolley is empty.

Getting started
Ready to give it a try and feel the benefits in your warehouse operations? Well, activating the barcode packing function is a breeze. Simply reach out to StoreFeeder support, and let the transformation begin.
Join the revolution
Don’t let outdated despatch processes hold your business back. Embrace the future with StoreFeeder’s barcode Packing function and watch your efficiency soar while errors and returns plummet.
By scanning barcodes during the packing process, you ensure each item is correctly assigned to the right order, drastically minimising the risk of errors.
Labels print only when all correct items are scanned, reducing costly returns.
This innovative tool streamlines workflow with unprecedented speed and precision, making manual matching and confusion a thing of the past.
When barcode packing is used in conjunction with picking through our app, (https://storefeeder.com/blogs/exploring-the-storefeeder-app-a-journey-through-pickwaves), the whole warehouse process is streamlined for efficiency, accuracy and minimising the chance of returns for mis-picked orders.
Contact StoreFeeder support today and take the first step towards a smarter, faster, and more reliable despatch process.