
Warehouse receiving: processes & best practices
August 28, 2024
Warehouse receiving is a crucial, yet often underestimated, component of efficient warehouse operations. As the initial touchpoint for incoming goods, it lays the groundwork for all subsequent supply chain activities. Unfortunately, many warehouses face common challenges during this stage, such as inaccurate inventory counts, receiving damaged goods, and processing delays. These issues can lead to significant disruptions, including inventory discrepancies, increased labor costs, and delayed shipments, which ultimately affect customer satisfaction and bottom-line profitability.
The impact of mislabeling or mishandling products can not only cause immediate operational headaches but can also result in long-term financial losses and damaged customer relationships. The stakes are high, and the pressure to get it right can be daunting.
But we have a solution, in our post, we'll delve into the best practices and innovative solutions that can transform your warehouse receiving process. From implementing advanced technologies to refining workflows and training staff, we'll provide you with actionable insights to streamline operations, reduce errors, and ensure a smooth and efficient receiving process. Whether you're looking to enhance accuracy, speed up processing times, or improve overall operational efficiency, this guide will equip you with the tools and knowledge to overcome the common challenges in warehouse receiving.
What are the processes involved in warehouse receiving?
Warehouse receiving encompasses a series of steps designed to verify, record, and organise incoming shipments effectively. These processes ensure accurate inventory management, efficient operations, and improved overall productivity by handling incoming goods systematically.
Step 1: Pre-receiving preparation
Scheduling deliveries and preparing the receiving area
Coordinating with suppliers to schedule deliveries is crucial for managing the workload and preventing congestion at receiving docks. By planning delivery times, warehouses can allocate resources efficiently, reducing the risk of delays and ensuring that staff are available to handle incoming shipments promptly.
A well-organised receiving area is essential for smooth operations. This involves cleaning the space, ensuring it is free from clutter, and equipping it with the necessary tools and equipment such as forklifts, pallet jacks, and scanning devices. Proper preparation of the receiving area facilitates the efficient unloading and processing of goods.
Verifying delivery documentation
Reviewing purchase orders and packing lists before shipment arrival ensures that the correct items and quantities are expected. This preliminary check helps in identifying discrepancies early, allowing for quick resolution.
Advanced shipping notices (ASNs) provide detailed information about incoming shipments before they arrive. Reviewing ASNs helps streamline the receiving process by allowing staff to prepare for specific items and quantities, thereby speeding up the inspection and documentation process.

Step 2: Receiving inspection
Unloading goods and inspecting for damages
Careful unloading of goods using appropriate equipment and techniques is essential to prevent damage. Staff should be trained in proper unloading procedures to handle different types of goods safely and efficiently.
Each item or pallet should be inspected for visible damages upon arrival. Documenting any issues immediately helps in addressing them with suppliers and ensures that only undamaged goods are processed further.
Verifying quantities and product specifications against the order
Counting received items and comparing them with the quantities listed on the purchase order and packing list is a crucial step. This process ensures that the warehouse receives the correct amount of stock.
It is important to check that received products match the specifications outlined in the purchase order. This includes verifying sizes, colours, and other specific attributes to ensure they meet the required standards.
Step 3: Receiving documentation
Recording received items in the inventory management system
Accurate data entry of received goods into the warehouse management system (WMS) is vital. This step ensures that inventory records are up-to-date and reflects the actual stock levels.
The WMS should update stock levels based on the received goods. This real-time update helps in maintaining accurate inventory records, facilitating better decision-making and inventory control.
Handling discrepancies and documenting any issues
Documenting discrepancies and contacting suppliers to resolve issues is a critical part of the receiving process. Prompt resolution of discrepancies ensures that inventory records remain accurate and prevents potential stock shortages or overages.
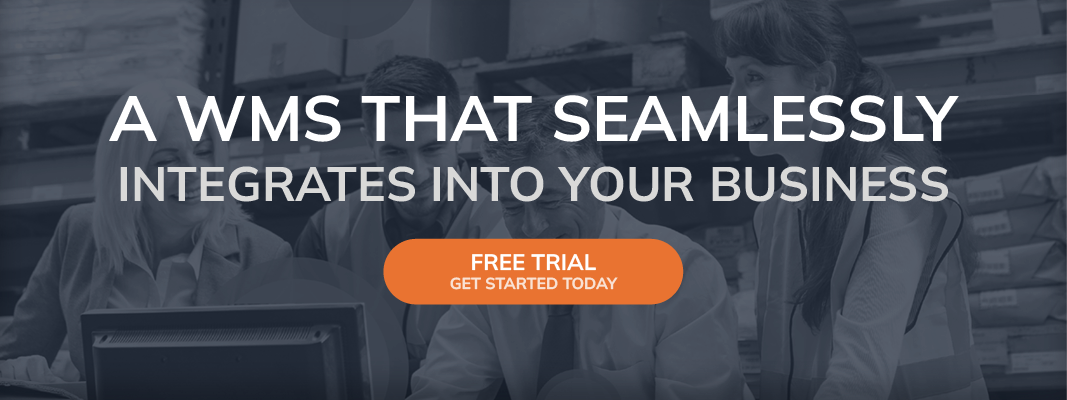
Keeping detailed records of any issues encountered during the receiving process is essential for tracking and resolution. This documentation helps in identifying recurring problems and implementing corrective measures.
Step 4: Product labelling and barcoding
Applying barcodes or labels to received products
Labelling each item or pallet with a barcode or identification tag is an important step in the receiving process. This ensures that products can be easily identified and tracked throughout the warehouse.
Using barcode scanning during the receiving process verifies items and prepares them for storage. This technology improves accuracy and efficiency in tracking inventory.
Proper labelling and barcoding are crucial for tracking items throughout their lifecycle in the warehouse. This traceability ensures that products can be easily located and managed, reducing the risk of errors and improving overall efficiency.
Step 5: Staging and putaway
Organising received goods for storage
A staging area is used to organise items based on storage requirements and priorities. This space allows for additional quality checks and ensures that goods are properly prepared for putaway.
Additional quality checks performed in the staging area help to verify that items meet the required standards before they are moved to storage locations.
Moving items to designated storage locations in the warehouse
The putaway process involves moving goods to their designated storage locations promptly. Efficient putaway practices ensure that items are stored in an organised manner, facilitating easy retrieval and maximising space utilisation.
Items should be stored to maximise space utilisation and ensure easy retrieval. Proper storage practices help in maintaining an organised warehouse and improving operational efficiency.
Updating the WMS to reflect new storage locations is essential. This ensures that inventory records are accurate and up-to-date, allowing for efficient management of stock.
Common mistakes with receiving to avoid

Warehouse receiving is prone to several common mistakes that can impact inventory accuracy, operational efficiency, and overall productivity. Addressing these mistakes is crucial for maintaining smooth warehouse operations.
Lack of preparation
A lack of a scheduled plan for deliveries, standardised procedures, and a well-prepared receiving area can lead to significant inefficiencies in warehouse operations. Without a structured schedule, managing the workload and preventing congestion at the receiving docks becomes challenging. Additionally, the absence of set procedures or a checklist for unloading and receiving can result in inconsistencies and errors. Furthermore, an inadequately prepared and disorganised receiving area can cause delays, further exacerbating inefficiencies in processing incoming goods.
Poor documentation
Poor documentation can significantly undermine warehouse operations, especially when there is a failure to verify and accurately record received items. This can lead to inventory discrepancies, causing operational inefficiencies and challenges in inventory management.
Additionally, ignoring discrepancies and neglecting to document issues can leave problems unresolved, further impacting inventory accuracy and potentially leading to customer dissatisfaction.
Inadequate inspection
Inadequate inspection practices can cause significant issues in warehouse operations. Skipping thorough inspections for damages and discrepancies may allow damaged or incorrect items to go unnoticed, resulting in complications down the line. Additionally, overlooking quality checks and ignoring product specifications can lead to substandard products being included in the inventory, potentially harming customer satisfaction and brand reputation.
Inefficient putaway processes
Inefficient putaway processes can significantly hinder warehouse operations. Delays in moving items to their designated storage locations can cause congestion in the receiving area, disrupting the flow of goods and impacting overall warehouse efficiency. Additionally, disorganised storage practices can lead to challenges in locating and retrieving items, reducing productivity and increasing the time required to fulfill orders.
Best practices for warehouse receiving
Implementing best practices for warehouse receiving enhances accuracy, efficiency, and productivity in warehouse operations. These practices ensure that receiving processes are streamlined and effective.
Implement standard operating procedures (SOPs)
Implementing standard operating procedures (SOPs) is crucial for streamlining warehouse receiving processes. Developing and adhering to detailed SOPs provides clear, consistent guidelines for staff, ensuring that each step of the receiving process is carried out accurately and efficiently. This consistency helps prevent errors and discrepancies, maintaining the integrity of inventory data. Additionally, regularly reviewing and updating SOPs ensures they remain relevant and effective, adapting to new challenges and evolving operational needs, thus continually optimising the warehouse's efficiency and effectiveness.
Leverage technology
Leveraging technology is essential for optimising warehouse operations. Utilising Warehouse Management Systems (WMS) allows for precise tracking of inventory, enhancing overall efficiency in stock management and reducing errors. Implementing barcode scanning and RFID technology further improves the receiving process by increasing the speed and accuracy of data capture. These technologies streamline the verification and recording of incoming goods, minimising the risk of discrepancies and ensuring accurate inventory management.
Training and communication
Training and communication are critical components of a successful warehouse receiving process. Providing comprehensive training for receiving staff ensures they are well-equipped with the necessary skills and knowledge to perform their tasks efficiently and accurately. Continuous training helps keep staff updated on best practices and new technologies. Additionally, fostering clear communication between the receiving team and other departments, such as inventory management and shipping, is vital. This coordination helps streamline operations, quickly address any issues that arise, and maintain smooth workflow throughout the warehouse, ultimately enhancing overall operational efficiency.
Continuous improvement
Continuous improvement is a key strategy for optimising warehouse receiving operations. Regularly reviewing receiving processes allows for the identification of inefficiencies and the implementation of necessary improvements, ensuring the process remains effective and efficient. Collecting feedback from staff who are directly involved in the receiving process provides valuable insights into practical challenges and areas for enhancement. By making adjustments based on this feedback, warehouses can refine their procedures, adapt to changing needs, and maintain high standards of operational performance.
Maintain a clean and organised receiving area
Maintaining a clean and organised receiving area is crucial for efficient warehouse operations. Keeping the area tidy and free from clutter not only facilitates the smooth processing of incoming goods but also reduces the risk of errors and accidents. Additionally, ensuring that all necessary tools and equipment are easily accessible allows staff to carry out receiving tasks quickly and efficiently, minimising delays and enhancing overall workflow. A well-organised receiving area contributes significantly to the accuracy and speed of inventory management.
Importance of efficient warehouse receiving practices
● Improved inventory accuracy: Reducing discrepancies and ensuring accurate inventory records are crucial for maintaining an efficient and reliable warehouse operation.
● Enhanced operational efficiency: Streamlining processes to minimise delays and bottlenecks enhances overall operational efficiency, allowing for faster and more accurate processing of incoming goods.
● Better supplier relationships: Handling deliveries smoothly helps maintain positive relationships with suppliers, ensuring reliable and timely supply of goods.
● Cost savings: Reducing errors and inefficiencies lowers operational costs, contributing to overall cost savings and improved profitability.
● Increased customer satisfaction: Timely and accurate order fulfilment is essential for meeting customer expectations and ensuring customer satisfaction.
How StoreFeeder can save you the work
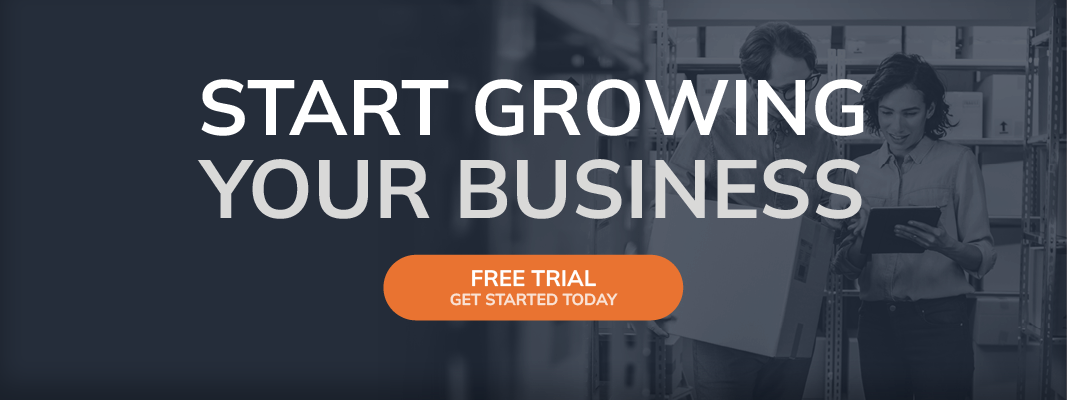
StoreFeeder offers an integrated solution to streamline your warehouse receiving and management needs, optimising your eCommerce operations with ease. Our advanced system simplifies the booking-in process, allowing you to receive goods from suppliers efficiently. Using our barcode technology, you can quickly scan products, input quantities, and locate them within your warehouse.
This ensures that as soon as an item is received and placed in its designated location, it is immediately ready for sale. For instance, if a batch of new inventory arrives, you can scan each item upon arrival, confirm the quantity, and have it automatically updated in your system, reducing manual entry errors and speeding up the entire process.
We encourage you to evaluate your current processes and consider adopting StoreFeeder's recommended practices and technologies. To learn more about how StoreFeeder can transform your warehouse operations, book a demo today at StoreFeeder.
Conclusion and next steps
Efficient warehouse receiving practices are the cornerstone of a well-functioning supply chain. As the initial point of contact for incoming goods, the receiving process sets the tone for all subsequent warehouse operations. By implementing best practices, such as standard operating procedures (SOPs), leveraging technology, and maintaining a clean and organised receiving area, you can significantly improve inventory accuracy, operational efficiency, and overall productivity. These improvements not only help in reducing costs but also enhance supplier relationships and customer satisfaction.