
What is Distributed Inventory Management (DIM) and how to implement it? | StoreFeeder
July 9, 2024
As eCommerce business owners, warehouse managers, and logistics and operations professionals, using traditional inventory management systems can pose several challenges.
These systems often struggle to adapt quickly to changes in demand or market conditions, limiting their flexibility. They provide insufficient visibility into real-time stock levels, hindering a business's ability to make informed decisions.
This lack of visibility can lead to stockouts, resulting in lost sales and decreased customer satisfaction, and overstocking, which increases storage costs and ties up capital. Additionally, traditional systems can lead to increased operational costs due to higher labour and storage expenses, and they may not integrate well with other business systems.
To address these challenges, businesses are increasingly turning to modern inventory management solutions such as Distributed Inventory Management (DIM).
DIM offers enhanced flexibility and responsiveness, helping companies quickly adapt to shifts and customer preferences. It provides improved visibility and control, offering comprehensive insights into inventory levels and reducing the risk of overstocking and stockouts. This, in turn, leads to faster order fulfilment and shorter delivery times, providing a competitive advantage.
In this blog post, we will explain DIM in detail, including its benefits and how it can enhance your inventory operations.
What Is Distributed Inventory Management (DIM)?
Distributed inventory management (DIM) is a strategy which involves storing and managing inventory across multiple locations instead of centralised inventory management, which keeps all stock in a single location. It encompasses several key concepts including:
● Multi-location inventory, which involves the strategic placement of inventory across various fulfilment centres, retail locations, and warehouses.
● Network optimisation, which involves analysing and optimising the entire distribution network to determine the best locations for inventory storage and the most efficient routes to fulfil these orders, which can balance costs, delivery times, and overall service levels.
● Real-time inventory tracking, which enables accurate stock monitoring.
DIM is essential for eCommerce businesses with a large, geographically diverse customer base. By using regional fulfilment centers and multiple locations, businesses can place products closer to customers, reducing shipping times and costs, and improving customer satisfaction.
Distributing inventory across various locations also minimises supply chain risks, and makes it easier to expand into new markets and handle cross-border fulfilment.
Core components of Distributed Inventory Management
Inventory allocation

Inventory allocation involves strategically distributing stock across multiple warehouses or fulfilment centres to balance supply with demand.
Predictive analytics and demand forecasting play crucial roles in determining optimal inventory placement in a DIM system by using advanced algorithms and machine learning models to analyse historical data and predict future demands.
This enables businesses to allocate inventory more effectively, anticipate changes in customer preferences, and ensure they are prepared to make informed decisions about inventory allocation based on the latest market conditions
Order routing
Order routing ensures that customer orders are fulfilled efficiently and cost-effectively. Orders are routed to the fulfilment centre closest to the customer's delivery address, minimising shipping distances, reducing delivery times, and lowering shipping costs.
Stock transfers
Stock transfers involve transferring stock between locations to maintain optimal inventory levels and meet shifting demands. The process typically involves identifying a need through analysing inventory levels and demand patterns, generating a stock transfer order (STO) specifying components such as quantity, source, destination, and the items themselves, and then packing, shipping, and receiving items.
Technology-powered logistics support efficient transfers in many ways as they can provide real-time visibility into stock levels, automate transfer requests, and use historical data to proactively identify transfer needs before stockouts. They can also use tools such as RFID, Transportation Management Systems (TMS), cloud-based systems, and Automated Storage and Retrieval Systems (AS/RS) to improve efficiency, accuracy, and speed.
For more detailed information on stock transfers and how to execute them efficiently, check out our dedicated post.
Technology integration
Technology integration plays a crucial role in managing distributed inventories. Warehouse management systems (WMS) provide real-time visibility, can optimise warehouse operations, enable efficient stock transfers, and offer advanced analytics. Whereas, inventory management systems (IMS) can track inventory levels, sales orders, and deliveries in real-time, automating reorder processes as well as providing insights into inventory turnover rates and enabling multi-location inventory management from a centralised platform.
Additionally, integration with eCommerce platforms and logistics can help synchronise inventory levels across online and offline channels, automatically update product availability on eCommerce storefronts, streamline shipping processes, and provide customers with accurate delivery estimates based on inventory location.
Benefits of Distributed Inventory Management
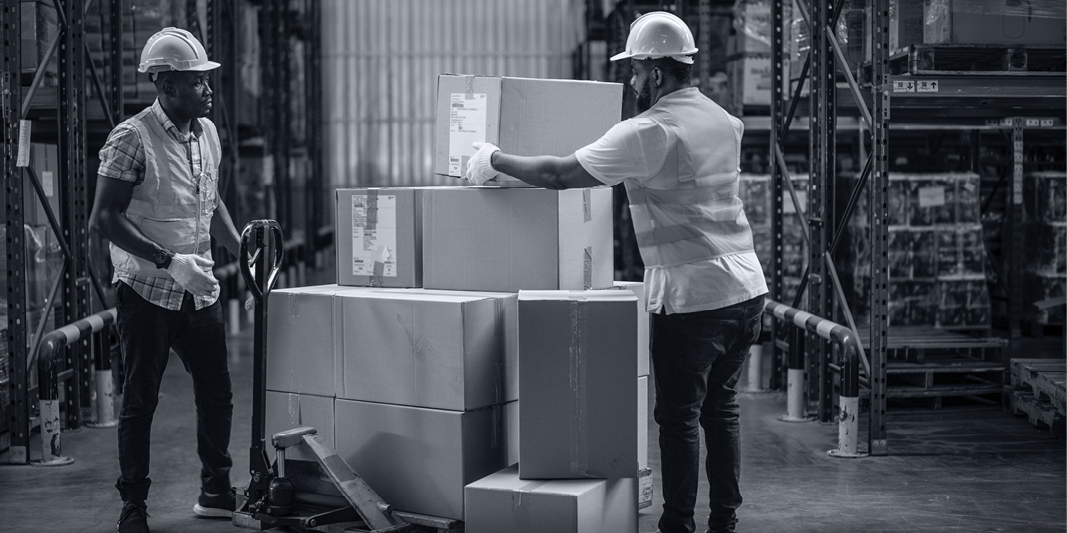
Distributed Inventory Management may seem a more complex system from the outside, however, there are several amazing benefits to this practice:
Improved delivery speed and customer satisfaction
Having inventory spread across multiple locations reduces delivery times by fulfilling orders from the nearest facility to the customer, providing an advantage in proximity. This means businesses can offer faster shipping options, directly impacting customer satisfaction, and arming themselves with a competitive advantage.
The ability to offer expedited shipping at lower costs has become a key differentiator, particularly in the eCommerce landscape. Customers expect fast delivery, and any business that can meet these expectations will often reap the rewards in the form of higher customer loyalty and repeat purchases.
Reduced shipping costs
DIM can significantly lower shipping costs by reducing the distance goods travel to reach customers through:
● Shorter last-mile delivery distances, which typically account for a large portion of shipping costs.
● The ability to use ground shipping more frequently instead of expensive air freight.
● Reduced fuel consumption and other associated costs due to shorter transportation routes. For example, a study conducted by Peerless Research Group reported an average 20% reduction in transportation costs.
Enhanced inventory flexibility
DIM allows businesses to respond quicker to changes in demand and supply chain disruptions through several components, including enabling the rapid reallocation of inventory between locations based on real-time demand data, as well as allowing for regional customisation of inventory based on local preferences and/or seasonal demands. This is particularly valuable during peak seasons, like holiday shopping or unforeseen events.
For instance, during COVID-19, retailers with distributed inventory were better able to manage stockouts and shifts in demand patterns compared to those relying on centralised distribution.
Better inventory utilisation
DIM leads to more efficient use of inventory as it reduces overstock through better demand forecasting and inventory allocation, as well as optimising stock levels across locations through real-time inventory tracking and analytics.
Real-time inventory tracking and analytics play a crucial role in this optimisation as they provide real-time visibility across all locations, allowing businesses to make data-driven decisions about inventory allocation and replenishment. By implementing this, businesses can achieve a balance between avoiding excess stock that ties up capital and having enough inventory to meet customer demand.
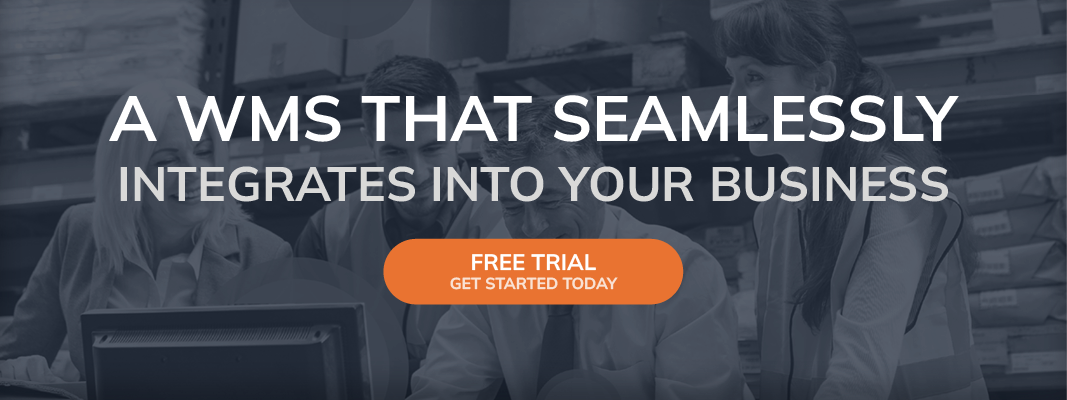
Challenges of implementing Distributed Inventory Management
Complexity of coordination
Managing inventory across multiple locations requires strong coordination and communication efforts to ensure consistent processes and standards across all facilities. StoreFeeder offers a centralised platform that provides real-time visibility into inventory levels across all locations, enabling standardised processes and workflows across all facilities, facilitating seamless communication and data sharing between locations, as well as automating inventory transfers and rebalancing based on predetermined rules.
Higher operational costs
Maintaining multiple storage facilities can result in increased costs and more complex logistics and transportation requirements, meaning the potential for redundancy in resources and inventory. StoreFeeder can balance costs by optimising inventory allocation to reduce overall stock levels, enabling efficient use of resources through automated processes and returns reporting, offering scalable solutions that grow with the business, and minimising unnecessary expenses.
Inventory visibility and control
Maintaining accurate real-time inventory data across a distributed network can be challenging. Ensuring consistent inventory control practices across facilities, and preventing stockouts and overstocking in a distributed network, can be supported through StoreFeeder as it enhances visibility and control through advanced tracking systems and real-time data analytics. Automated alerts for low stock levels, as well as centralised reporting, can offer a comprehensive inventory oversight.
Integration with existing systems
Integrating a DIM solution with existing warehouse, order management, and leadership systems can be challenging due to data synchronisation, system compatibility, process alignment, and scalability, as well as other issues like educating staff, cost considerations, security, and ongoing maintenance. To address these challenges, conducting system audits and choosing DIM solutions with robust pre-built integrations can be the best solution.
StoreFeeder facilitates seamless integration by offering flexible APIs, providing dedicated support for custom integrations and data migration, as well as ensuring data consistency through robust validation and synchronisation processes.
Steps to implementing Distributed Inventory Management

Step One: Assessment and planning
At this stage, it is wise to do the following:
● Assess current inventory and fulfilment processes.
● Determine DIM suitability through geographic distribution of customers, order volumes, and product characteristics.
● Set clear objectives and establish KPIs to measure success.
● Conduct a cost-benefit analysis to estimate potential savings in shipping and handling.
Step Two: Choosing the right technology
● Select a robust WMS (Warehouse Management System) with features such as real-time inventory tracking and multi-location support to ensure scalability to accommodate future growth.
● Implement advanced inventory management systems (IMS) with demand forecasting and inventory optimisation capabilities while ensuring compatibility with existing software.
Step Three: Designing the distribution network
● Analysing customer data at this point can identify optimal locations for fulfilment centres through data analytics.
● Plan inventory allocation through the right strategies for distributing inventory across locations, while also using historical sales data and predictive analytics to optimise stock levels.
● At this stage, you should also identify reliable shipping partners and establish transportation networks with appropriate rates and service level agreements.
Step Four: Integration and execution
● When integrating DIM with existing operations and systems, it's vital to ensure seamless data flow between the WMS, IMS, OMS, and other systems and test the integration thoroughly prior to full implementation.
● Pilot testing can be an excellent method at this stage to help refine processes and gather data, and when doing this, start with a limited product range or geographic area.
● Providing comprehensive training for staff on new systems and processes while also developing standard operating procedures for each location also ensures a comprehensive understanding.
● When rolling out DIM, it's essential to implement it in stages to minimise disruptions while continuously monitoring performance and adjusting as needed.
● Regularly reviewing KPIs and adjusting strategies as necessary will help identify areas for improvement so you can establish a system focused on monitoring and optimisation.
● Finally, you should be prepared to adjust the network design as the needs of your business evolve, and regularly reassess the effectiveness of each fulfilment location.
How StoreFeeder can save you the work
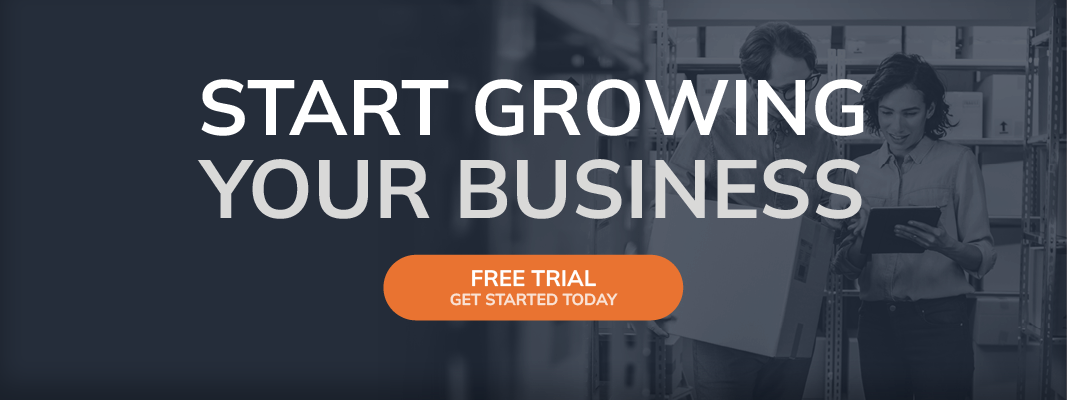
StoreFeeder supports your Distributed Inventory Management needs and help you optimise your eCommerce operations through many significant benefits:
● Centralised control of your Distributed Inventory Management system, which eliminates the need for manual data entry across different systems, saving time. For example, a retailer with inventory in three different warehouses and selling on five online marketplaces can easily view and manage all stock levels from one dashboard.
● StoreFeeder offers real-time visibility into inventory levels across all locations to prevent overselling and stockouts. For example, when an item sells out in one warehouse, StoreFeeder automatically updates stock levels across all connected sales channels, preventing overselling and potential customer disappointment.
● StoreFeeder's intelligent order routing system automatically assigns orders to the most appropriate fulfilment location based on factors like shipping costs, delivery times, and inventory availability. For example, if an order is placed by a customer in York, it's automatically routed to the nearest warehouse with available stock, reducing delivery times and transportation costs.
● StoreFeeder's multi-currency functionality allows businesses to manage inventory and transactions in different currencies.
● StoreFeeder's integration with other business tools including popular eCommerce platforms like Shopify, as well as accounting software and shipping carriers, ensures data consistency across all systems.
● Insights to track sales performance and other business metrics, ensuring businesses make data-driven decisions to optimise their operations.
● Barcode scanning technology to improve accuracy and efficiency in warehouse operations.
● Tracking of serial numbers, which is particularly useful for high-value goods or products which require warranty tracking.
Implementing the strategies and tips we've provided can result in significant improvements in your productivity and cost savings.
Using StoreFeeder can help you improve operational efficiency, reduce costs, and ultimately enhance customer satisfaction. It's more vital than ever to evaluate your current processes.
At StoreFeeder, we're here to help you enhance your warehouse operations. Contact us today to book a demo or sign up for a free trial and see how the wealth of hands-on experience built into the StoreFeeder WMS can offer your business real-time benefits.